Work with Horsent today to save
Horsent production dept Responsible for the centralized management of the touch screen manufacturing process;
Each production process shall apply appropriate equipment and calibrated monitoring and measuring equipment; Labeling and save products to ensure traceability; Organize the production according to the production plan.
Our First class product line is capable of producing touch screen monitors and all in one 210,000sets annually
We update the standard operation process(SOP) whenever there is an issue, improvement or even doubt.
Running against SOP to meet the speed of production is definitely against our values.
From Touch panel Assembling, Frame assembling, to PCB, LCD embedded, plate and housing installation plus ageing
Our Lines have been managed as per ISO9001-2015, as Productive, Efficient, Cost-competitive, Safe and Massive.
Touch Panel Assembling.
Horsent use 3M tapes to assemble the touchscreen panel.
Before that, we tested and confirmed the capacity and adhesive of the tapes and whether they can withstand the monitor overtimes in real touchscreens applications.
We apply different categories for each different touch panel and monitor size, even different gap filling and we ensure use of the corresponding tape for every kind of our product.
Horsent balanced with the tapes and breath cotton, with firm adhesive still air the structure of the touchscreen panel to the LCD to avoid condensation
LCD integration
Horsent owns a 20m2 clean room with full set equipment and facilities for LCD to Touch Panel assembling.
4 Work stations in clean rooms for assembling+ and dust cleaning, and one station for final cleaning after assembling.
Our engineering Dept checks and inspect the equipment and facilities such as airflow, wind blow and environment of temperature and humidity at regular basis
to ensure a clean and critical environment and smooth operations for LCD and inside of touchscreen monitor.
Finally, Horsent achieves a 6S standard cleanroom for safe and productive production.
PCB assembly
Horsent has 8 workstations for PCB assembling, including AD Board, touchscreen controller board, and PCBs of touchscreens all in one.
Each PCB is managed under systems both the online system process and the downline, to ensure the full tracking of each PCB and its installations.
The engineering depts check the equipment and facilities at regular basis to ensure safe operations and smooth running.
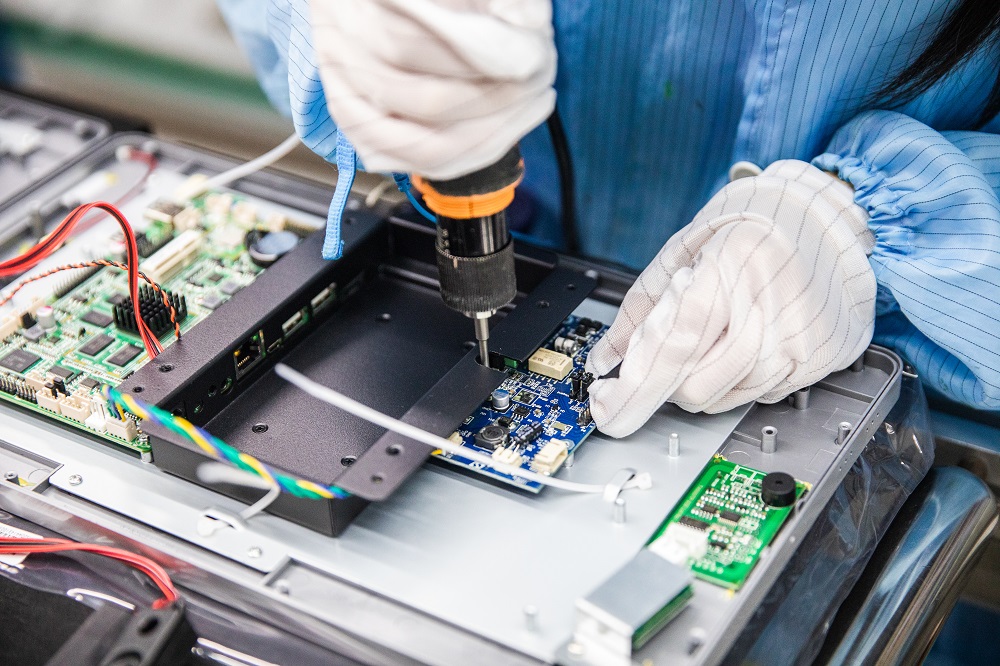
Structures installation
Horsent sets 8 workstations for Structures installations
including plats, frames, and housing...both open-frame touchscreens and touchscreen monitors.
in order to achieve firm structures inside the touchscreen monitor for smooth running, still rich spacing for air and heat.
outside, Horsent is willing to build a safe and durable casing and housing to protect touchscreen from the heat, dust and force.
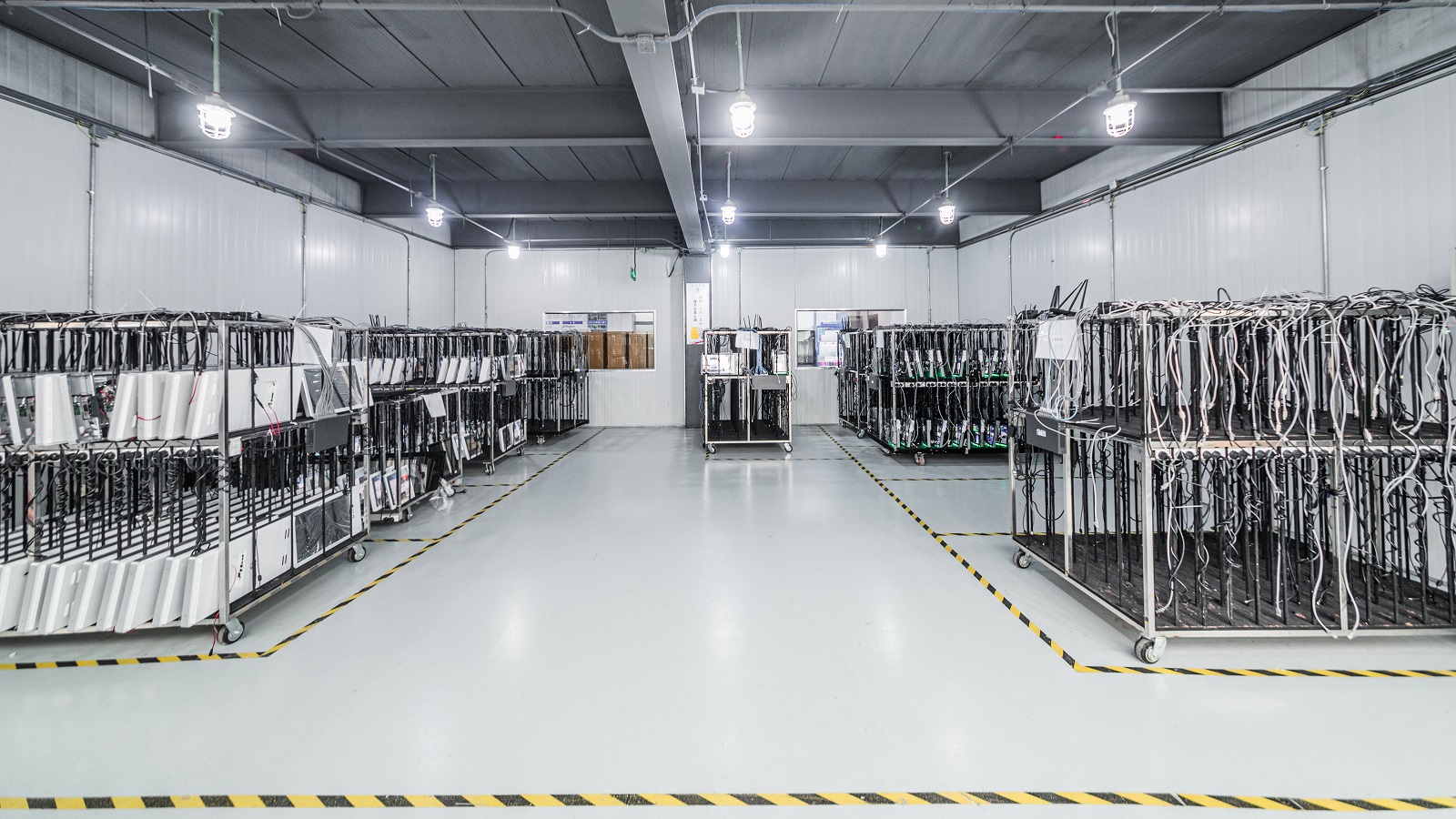
Curing & Ageing
To achieve an earlier exposure of the issue and NG product, that runs into the market, Horsent built a 60m2 independent room for curing and aging of all touchscreens monitor and touchscreen all in ones.
4~8 hrs of curing will expose most of the potential and risks of our product before the inspection of vision and functions.
Horsent engineering check and ensure the environment of curing room is close to the real environment of touchscreen applications.